JBS Group charts record growth with 38% surge in turnover
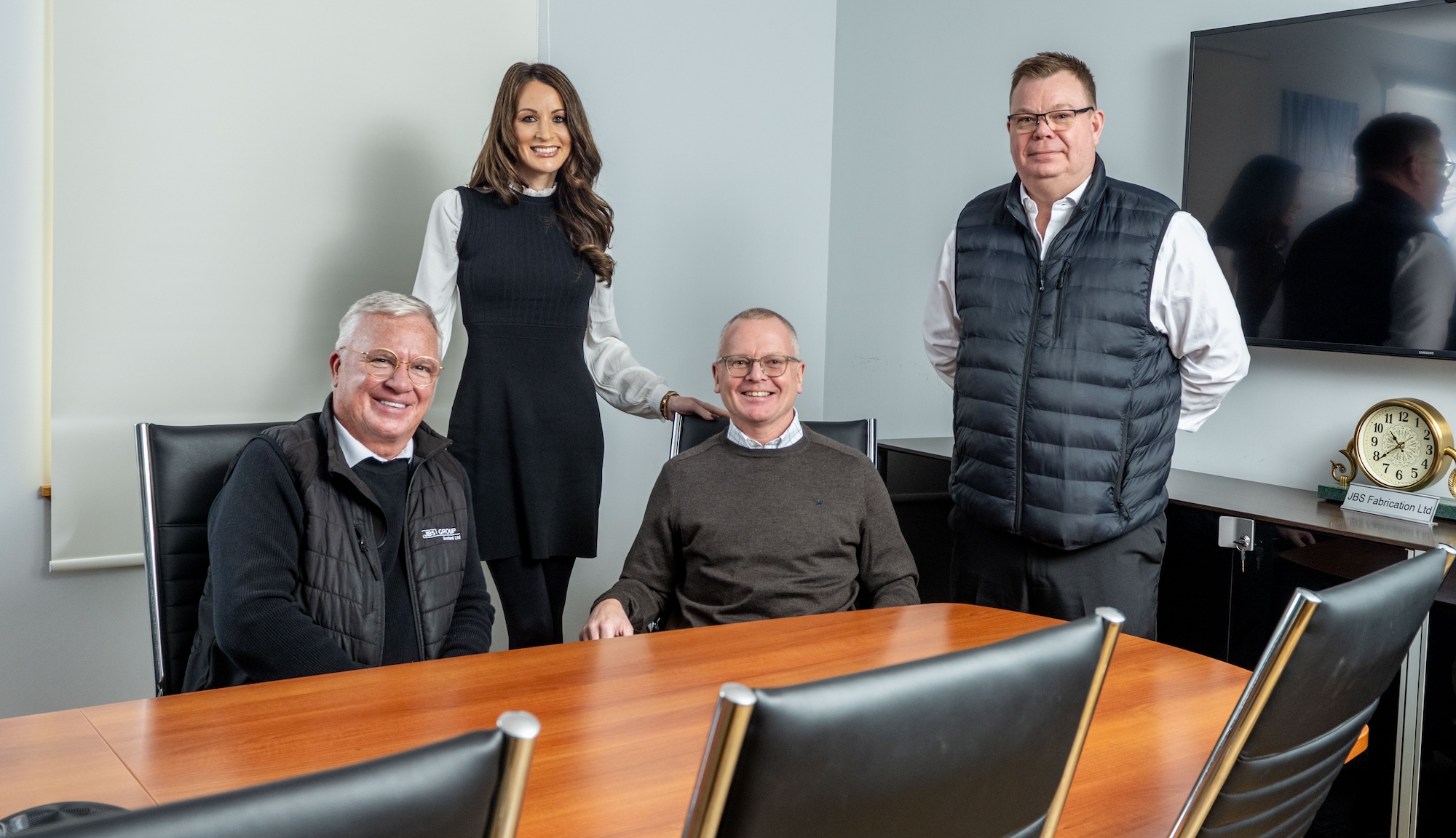
Pictured (L-R): JBS' operations director Alex Whyte, sales & marketing director Jo McIntosh, managing director Mike McCafferty, and general manager Gordon Milne
Peterhead-based engineering business JBS Group has achieved a turnover of £11.5 million for the year ended 30 April 2024 – up from £8.3m for the same period last year.
The firm has secured a plethora of contracts in the UK and internationally, with clients including operators, global engineering firms, large subsea firms, US space giants and specialist North Sea engineering companies.
Jo McIntosh, sales and marketing director, said: “Our broad range of products and services, supported by a proven track record, are reaping dividends. We are securing complex engineering projects in the UK and internationally that are challenging but also rewarding.
“International work now accounts for more than 60% of our projects and we expect this to increase over the next financial year. We can continue to grow by continuing to provide valuable support to client projects and expanding our capability into other markets beyond the energy sector.”
JBS Group has four main divisions – fabrication, its innovative Sea Axe subsea excavation technology, blast containment systems, and screw conveyors.
The firm has seen increased global demand for its Sea Axe Controlled Flow Excavation (CFE) technology, known for its compact design and environmentally friendly approach to subsea excavation. This method, which leverages natural erosion, minimises impact and meets the growing client demand for sustainable and innovative solutions. The patented technology has secured UK and international contracts,
The fabrication division has also seen a rise in demand, resulting in numerous contracts with large energy firms. This work spans reel modifications, on-site fabrication support and other specialised services.
JBS has secured agreements with various companies in the energy and space sectors for its unique blast containment products. These products, featuring patented fabrics, offer protection against ballistic, blast, fire and arc flash hazards.
The group has also supported replacement part programmes and the implementation of its proprietary dual-drive screw conveyor systems. One specialist project was a twin conveyor system with shaftless screws and xylethon liners. These were engineered and designed specifically for challenging drilling muds where previously traditional conveyors had failed.